Your shopping bag is empty.
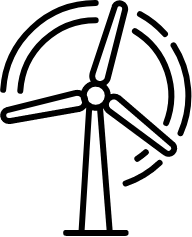
Adopt renewable energy commitments by the end of 2022 .
We manufacture our core down-filled parkas across Canada in eight owned and operated facilities in Montreal, Toronto, Scarborough, and Winnipeg. Going into 2020, we employed 4,591 workers in Canada – one-fifth of the Canadian garment-making sector’s workforce. By keeping the majority of our production domestic, we contribute to local job growth and can more easily maintain our high manufacturing and labour standards.
Canada Goose also prides itself in only working with the best global partners in our product supply chain. As we add new apparel categories to our lineup, such as knitwear and accessories, we do extensive research to find the right manufacturers – the ones who are capable of meeting our quality expectations and rigorous social and environmental standards.
At home and abroad, in addition to sourcing the best, we prioritize continuous improvement. We are constantly imagining and implementing new ways to care for both people and the environment.
Whether they work in Canada or abroad, at our factories or for our suppliers, the people who make our garments are part of the extended Canada Goose family. Through the Canada Goose Social Performance Program, we take measures to protect and respect the people
During 2020, we focused on setting the foundation for a stronger, more collaborative version of the Social Performance Program. This included updating our Supplier Code of Conduct. The Code sets out our standards for working conditions and environmental responsibility throughout our supply chain. It applies to contractors, manufacturing partners, and their factories that we manufacture with directly or indirectly. We’ve also developed supplemental materials that provide all suppliers with valuable guidance and a transparent view into our Social Performance Program policies, procedures, and supplier assessments.
All offshore and domestic suppliers, as well as Canada Goose owned and operated facilities, signed the updated Supplier Code of Conduct in 2020.
Alongside PFM education, we’ve updated our warehousing system, developed new IT processes for managing documentation, and evolved our Raw Materials Supply Chain Map, an internal tool designed to give us a clear view of what’s going on in our supply chain.
Assessing and improving compliance
Our program includes periodic social self-assessments and third-party assessments; we initiate ongoing collaboration and open dialogue with our suppliers to deliver on our commitment to responsible manufacturing.
Our suppliers are true partners – we give and receive mutual support. If a supplier or one of their factories becomes non-compliant with any of the principles and guidelines in our Supplier Code of Conduct, we take an active role in helping them immediately address and improve their practices.
During the pandemic, we needed to reapproach our plan for assessing compliance with our updated Code. We gathered third-party assessments
for the factories that had them, and all suppliers completed a self-assessment. We are continuing to work with suppliers to evaluate their social performance. Through the updates to our Social Performance Program, we’re creating a framework for strong partnerships that will motivate suppliers not only to meet our standards but to continuously improve their processes. Together, we can make a more significant impact for safe, inclusive, responsible workplaces within our network.
Protecting human rights
We believe that business should support and respect the protection of human rights. At Canada Goose, we do not tolerate any human rights abuses including child labour; forced/prison labour, slavery, or human trafficking; verbal, emotional, or sexual harassment/abuse; bribery and associated practices; and falsified documentation.
Connected with opportunity Manuela S., Canada Goose Floor Trainer, Toronto
Twelve years ago, Manuela was making men’s suits for another company. “My sister-in-law was always talking about benefits she had at Canada Goose that I didn’t have with my employer,” she said. “So when I was laid off, I had no question about it. I went straight to Canada Goose to apply.” She got the job and started in the production line.
Manuela appreciates the opportunities at Canada Goose to try out new roles and advance her career. From the line, she soon moved to warranty repairs, where she stayed about five years. Now she’s a floor trainer who helps machine operators learn new styles each time their production line is updated.
Last year, Manuela trained operators in something completely new for Canada Goose – personal protective equipment. “It’s something that makes you feel good,” she said. “I am proud of Canada Goose for the opportunity to help front-line workers be safe.”
“I intend to keep working here,” she added. “There are always different things to do. We have a good environment inside, good supervisors, good benefits. This is a good company.”
Whether they work in Canada or abroad, at our factories or for our suppliers, the people who make our garments are part of the extended Canada Goose family. Through the Canada Goose Social Performance Program, we take measures to protect and respect the people who make our products.
During 2020, we focused on setting the foundation for a stronger, more collaborative version of the Social Performance Program. This included updating our Supplier Code of Conduct. The Code sets out our standards for working conditions and environmental responsibility throughout our supply chain. It applies to contractors, manufacturing partners, and their factories that we manufacture with directly or indirectly. We’ve also developed supplemental materials that provide all suppliers with valuable guidance and a transparent view into our Social Performance Program policies, procedures, and supplier assessments.
All offshore and domestic suppliers, as well as Canada Goose owned and operated facilities, signed the updated Supplier Code of Conduct in 2020.
Alongside PFM education, we’ve updated our warehousing system, developed new IT processes for managing documentation, and evolved our Raw Materials Supply Chain Map, an internal tool designed to give us a clear view of what’s going on in our supply chain.
Assessing and improving compliance
Our program includes periodic social self-assessments and third-party assessments; we initiate ongoing collaboration and open dialogue with our suppliers to deliver on our commitment to responsible manufacturing.
Our suppliers are true partners – we give and receive mutual support. If a supplier or one of their factories becomes non-compliant with any of the principles and guidelines in our Supplier Code of Conduct, we take an active role in helping them immediately address and improve their practices.
During the pandemic, we needed to reapproach our plan for assessing compliance with our updated Code. We gathered third-party assessments
for the factories that had them, and all suppliers completed a self-assessment. We are continuing to work with suppliers to evaluate their social performance. Through the updates to our Social Performance Program, we’re creating a framework for strong partnerships that will motivate suppliers not only to meet our standards but to continuously improve their processes. Together, we can make a more significant impact for safe, inclusive, responsible workplaces within our network.
Protecting human rights
We believe that business should support and respect the protection of human rights. At Canada Goose, we do not tolerate any human rights abuses including child labour; forced/prison labour, slavery, or human trafficking; verbal, emotional, or sexual harassment/abuse; bribery and associated practices; and falsified documentation.
Protecting human rights
We believe that business should support and respect the protection of human rights. At Canada Goose, we do not tolerate any human rights abuses including child labour; forced/prison labour, slavery, or human trafficking; verbal, emotional, or sexual harassment/abuse; bribery and associated practices; and falsified documentation.
Canada Goose was born in the North. It is here that the world witnesses the impacts of climate change as permafrost melts, glaciers recede, and animal migration patterns change. And it is here that we draw inspiration for reducing our environmental impact as we learn from the example of indigenous people who respectfully live in harmony with nature.
Over the past two years, we’ve undergone third-party waste and energy audits that used carbon footprinting exercises and in-depth analyses to reveal our environmental “hot spots.” The findings are helping us chart our own path toward operating in greater harmony with the environment.
Across our business, we’re making progress in energy use, carbon emissions, and waste. Our Sustainability Councils around the world are leading efforts to implement region-specific facility improvements that include centralized waste collection, alternatives to conventional single-use plastic items, and environmentally friendly cleaning supplies.
Energy for improvement
In 2019, we conducted our first carbon footprint exercise of Scope 1 and 2 emissions and identified the energy hot spots across our organization – the locations with the largest gaps between where we were and where we want to be. In early 2020, we took the next step by conducting energy audits at those hot spot locations. The results provided clear guidance on renewable energy, renewable energy credits (RECS), and energy efficiency improvements we need to make over time. This combination will create the greatest impact on our global energy use and position us to meet our carbon emission goals.
At the global scale, we have committed to:
Adopt renewable energy commitments by the end of 2022 .
Invest in energy efficiency and renewable energy purchases and/or installation by 2023.
Invest in renewable energy credits as needed until 2025.
Adopt renewable energy commitments by the end of 2022 .
Invest in energy efficiency and renewable energy purchases and/or installation by 2023.
Invest in renewable energy credits as needed until 2025.
The North Star of net zero
We have set an ambitious goal to support the world’s urgent need to mitigate the impacts of climate change:
Achieve net-zero Scope 1 and 2 emissions by the end of 2025 or sooner
Our path to net zero requires us to boldly transition from conventional to renewable energy sources – and it requires that every type of Canada Goose facility take the journey together. To help our many facilities keep pace with each other, we are …
Conducting energy audits when identified as a need to highlight required energy-saving procedures Implementing purchase procedures that eliminate the use of traditional lighting, space heaters, and other energy-intensive equipment
Conducting energy audits to highlight required energy-saving-opportunities.
Eliminating the use of traditional lighting by upgrading to LEDs in all of our manufacturing facilities (completed in 2020) as well as utilizing sophisticated Lighting Control Systems that include motion sensors.
Updating real estate policies to require green lease agreements
Focusing on LEED® certified development
Developing requirements for no/low-carbon energy purchases and facility retrofits
We’re working as quickly as we can to secure renewable energy purchases and reduce our emissions, but we know climate action can’t wait. So, each year until we reach our goal, we’re investing in projects that reduce, avoid, or sequester the equivalent of 200% of our annual Scope 1 and 2 greenhouse gas emissions. In 2020, we began working with third-party firm Carbon Zero to develop a strategic, long-term offset project that will align with our overall strategy.
Carbon emissions: where we’re at
Between 2019 and 2020, we expanded our global operations by adding 11 new locations, increasing square footage at some existing manufacturing facilities, and installing cold rooms at various retail sites. As expected, our combined Scope 1 and 2 GHG emissions increased – although by 5% more than we had planned for. We’ve learned more about balancing efficiency and growth from this. And during 2021, we are ready to accelerate our progress to stay on track toward our 2025 goal.
As the circular economy grows in the apparel industry, we’re exploring new and innovative ways to reduce, reuse, and recycle across all areas of our operations. In early 2020, we conducted waste audits at all of our owned and operated facilities, including our head office and raw materials warehouse.
From the results, we realized a significant part of our impact could be reduced by improving waste, recycling, and organics hauling partnerships. Over 2020, we tackled waste related to single-use plastics, surplus fabric, electronic waste, products that don’t meet our quality standards, and warranty returns. Additionally, we formed a Sustainable Packaging Working Group to create an all-in approach to converting our existing packaging to more sustainable (and stylish) options for our consumers
Read about three key areas for waste reduction >
Single-use plastics
We had committed to eliminate single-use plastics that we cannot recycle (such as shrink wrap) in all facilities that we own or control by the end of 2020. While world events made this challenging, the waste audits enabled us to estimate the single-use plastic benchmark for those facilities and provided a starting point for us to benchmark all other facilities by using surveys. The benchmarks are being used to help facilities teams and their regional Sustainability Councils implement region-specific solutions, including standardized, centralized waste collection systems and reusable or compostable alternatives to conventional single-use plastic items.
E-waste
We’re doing our part to keep electronics out of Canada’s landfills. Each year, partners such as Lifespan Technology and eCycle Solutions collect and responsibly recycle the electronics we can no longer use. Laptops, keyboards, mice, cell phones, and copper data cables are among the many items they accept. These companies are R2 Certified as responsible recyclers. They reclaim precious metals and minerals and sell parts, ensuring no piece of our electronics ends up where it doesn’t belong – in a landfill
Warranty waste
We stand by our lifetime warranty. When we replace a product under warranty, we keep the product that was returned. That non-functioning product is referred to as “end-of-life warranty waste” – but we don’t think it should actually go to waste
In the textile industry, it is no secret that a common practice is to send textile waste for destruction by incineration or landfilling. We want to do things differently, so we’ve committed to developing strategies for recycling, reusing, and upcycling our unused and post-warranty materials and products. >
Throughout 2020, we partnered with textile recyclers in Canada, the U.S., and Europe to conduct trials for various recycling, donation, and re-commerce options for our warranty waste. One trial partnership alone diverted nearly 6000 parkas for recycling in the U.S. By the end of 2020, we were working on a global diversion strategy – and we’re excited to take on the work to change the channel on waste.
Meeting our goal of using reclaimed fur trims will also help us reduce warranty waste. When parkas are returned to us for warranty claims, fur trims that are in good condition can be removed, refurbished and prepared for reuse, and applied to new products.
“Innovation is at the core of everything we do. Our approach is driven by constant improvement – testing, learning, improving – while ensuring we deliver on our commitment to quality and functionality. We innovate for the betterment of our consumers and our planet.”
Innovation comes naturally to Canada Goose employees – it’s embedded in our values. Even in a year like 2020 – or perhaps especially in a year like 2020 – our people pursued new ideas and turned new processes into long-term strategies for efficiency.
Read about ways we upped our efficiency and reduced waste in 2020.
“Innovation is at the core of everything we do. Our approach is driven by constant improvement – testing, learning, improving – while ensuring we deliver on our commitment to quality and functionality. We innovate for the betterment of our consumers and our planet.”